人工智能如何推动制造业的设备智能化管理
2025-03-11
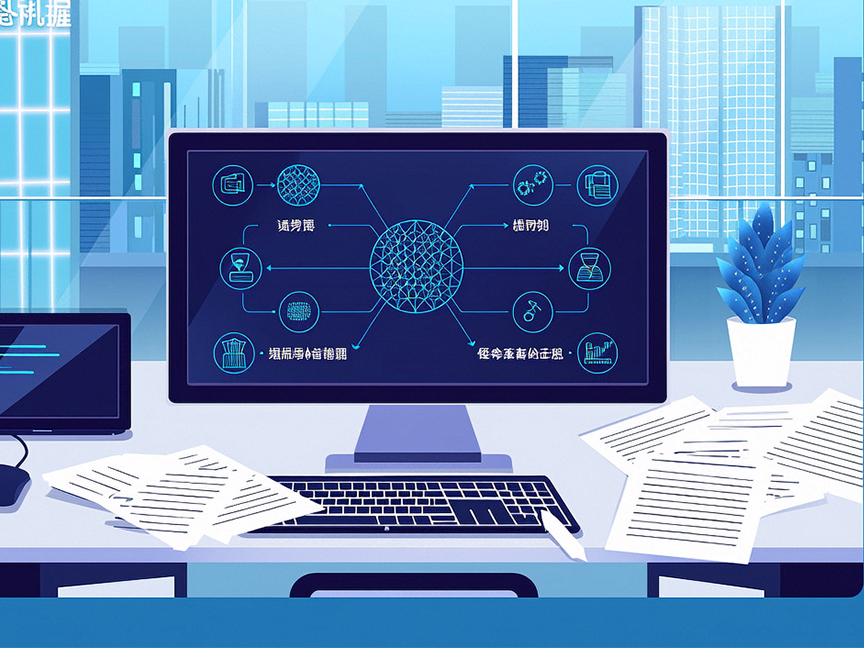
人工智能技术的迅猛发展正在深刻改变着制造业的传统模式,尤其是在设备智能化管理方面展现出了巨大的潜力。通过引入人工智能算法和智能系统,企业能够实现对生产设备的全面监控、预测性维护以及优化生产流程等关键功能,从而显著提高生产效率和产品质量。
一、实时监测与数据分析
在传统的制造业中,设备的状态监测往往依赖于人工巡检或简单的传感器报警机制。这种方法不仅效率低下,而且容易出现误报或漏报的情况。而借助人工智能中的机器学习算法,可以构建起更加精准高效的设备状态监测系统。
- 多源数据融合
- 制造业设备通常配备了多种类型的传感器,如温度传感器、压力传感器、振动传感器等。这些传感器采集的数据包含了设备运行的丰富信息。人工智能算法能够将来自不同传感器的海量数据进行融合处理。例如,在一个大型机床设备上,通过对温度、振动频率、切削力等多个参数的数据进行综合分析,可以更准确地判断设备是否存在潜在故障风险。
- 多源数据融合还能够弥补单一传感器数据的局限性。某些情况下,单个传感器可能会受到环境因素干扰而产生异常数据,但当与其他传感器数据结合分析时,就可以有效排除这种干扰,提高监测结果的可靠性。
- 异常检测
- 基于机器学习模型(如支持向量机、神经网络等),可以从正常设备运行数据中学习出特征模式。一旦设备运行过程中出现偏离正常模式的数据,即被判定为异常情况。例如,在电机设备中,正常运行时电流波动有一定的规律范围。如果突然出现电流急剧增大或者周期性的不规则波动,机器学习模型就能及时识别并发出警报,提醒工作人员检查电机是否存在过载、短路等问题,避免故障进一步扩大。
二、预测性维护
预测性维护是设备智能化管理的核心内容之一,它改变了传统的事后维修或定期预防性维修模式,实现了根据设备实际状况进行维护的最佳策略。
- 故障预测
- 人工智能通过深度学习算法挖掘设备历史故障数据与运行数据之间的关联关系。以航空发动机为例,研究人员收集了大量关于发动机部件磨损、疲劳损伤等故障案例以及对应的飞行时间、推力、燃油流量等运行数据。利用深度学习网络(如卷积神经网络)对这些数据进行训练后,可以建立起发动机故障预测模型。该模型能够提前数周甚至数月预测出发动机可能发生故障的时间点和具体部位,使得航空公司可以在最佳时机安排维修工作,降低维修成本的同时提高了航班的安全性和准点率。
- 维护计划优化
- 在确定了设备可能出现故障的概率和时间之后,人工智能系统可以根据企业的生产计划、库存情况等因素制定出最优的维护计划。对于汽车制造工厂来说,生产线上的机器人手臂是关键设备。当预测到某台机器人手臂即将发生故障时,系统会考虑当前订单的紧急程度、备件的供应周期以及技术人员的可用性等因素。如果当前订单较为紧迫且备件充足,技术人员有足够的时间进行维修,则可以选择在不影响生产进度的情况下提前安排维护;反之,如果订单不紧急,则可以适当推迟维护时间,确保资源得到最合理的利用。
三、生产流程优化
设备智能化管理不仅仅是针对单个设备的维护和管理,更是要将设备融入到整个生产流程中进行协同优化。
- 设备间协同调度
- 在现代化工厂中,众多设备之间存在着复杂的交互关系。人工智能可以通过模拟仿真技术建立虚拟的生产环境,分析各个设备的工作状态、任务分配等情况。例如,在电子芯片生产车间,光刻机、蚀刻机、离子注入机等多种设备需要按照特定的工艺流程顺序作业。人工智能系统可以根据产品需求、设备性能差异等因素,动态调整设备之间的作业顺序和参数设置,使整个生产流程更加流畅高效,减少设备等待时间和物料周转时间。
- 能耗管理
- 设备的智能化管理也涉及到能源消耗的优化。许多制造业设备在运行过程中消耗大量的电力、水、气等能源。通过安装智能电表、水表、气表等计量设备,并结合人工智能算法分析设备的能耗模式。对于注塑成型机而言,其加热系统的能耗占比较大。人工智能可以根据产品的尺寸、形状、材料等因素,精确控制加热功率和时间,避免不必要的能源浪费,同时保证产品质量不受影响。此外,还可以根据不同季节、时段的电价波动情况,合理安排设备的开机时间,降低企业的生产成本。
总之,人工智能为制造业设备智能化管理带来了前所未有的机遇。随着技术的不断发展和完善,未来的人工智能将在设备智能化管理领域发挥更加重要的作用,推动制造业向着更加智能、高效、绿色的方向发展。
